How do you know if you’re truly improving quality and efficiency in your manufacturing operations? Do your operations managers know if your equipment is as effective as you think it is? Are your operating lines a bottleneck in getting orders delivered to your customers? How would you demonstrate that?
You may have broad goals of increasing profitability and being more efficient at production, but if you’re not measuring your operations today in terms of more than just production counts, then you likely have no way of knowing how well you are progressing toward those goals.
Knowing what to measure is key, but where should a manufacturer begin, specifically in operations? Through implementing impactful technology solutions, we have seen there are many key performance indicators (KPIs) that manufacturers should be tracking. For this post, let’s look at just ten performance metrics centered around three strategic business goals: improving quality, improving operational efficiency, and increasing profitability.
Improve Quality
1. Yield
Sometimes referred to as First-Pass Yield, this measure helps you determine how effective your process is at not producing waste. Yield is the ratio of sellable product produced in a period to the total number of products produced in that same period (Sellable Product / Total Product). To track Waste (also called Scrap), use the inverse (Unsellable Product / Total Product).
2. Customer Return Rate
The rate at which products are returned by the customer as defective is a measure that ties in customer satisfaction with quality in production (Units Returned as Defective / Total Units). You’ll only be able to realize this measure if you have a way of tying specific products back to a production run through something like a lot number or license plate (and we can help you with that).
Improve Efficiency
3. Availability
Of all the time available in a production run, how much of that time were you actually making product? The amount of run time over the total period is the Availability percent (Run Time / Total Time). Running non-stop would be a 100% Available machine and no Downtime.
4. Throughput
Here we are trying measure how much a crew, machine, plant, etc. produced within a specific amount of time (Quantity Produced / Time). This gives you an idea of what is possible for production, but if you compare this over time against similar variables (crew, product SKU, period) or against a benchmark, then you’re able to gain valuable operational feedback!
5. Capacity Utilization
You may think you don’t have an under-utilized asset, but this operational KPI helps us get back to reality. It can be measured by comparing the potential volume of product that can be made in each production run with the actual production count (Actual Volume / Potential Volume). You’ll know if there is under-utilization if the percentage is less than 100%. Then you can look at factors such as reasons for downtime, reasons for waste, shift turnover time, etc.
6. Mean Time Between Failure (MTBF)
One key way to improve efficiency and increase output is by increasing the amount of time between machine failures. This is calculated by averaging the time between machine failures (Total Time Between Failures / Number of Failures). Monitoring this key metric will help you focus your maintenance efforts as well as realizing a higher output as you increase MTBF.
7. Performance
If you’re able to calculate the Throughput KPI, then the next step would be to compare your Throughput against a standard Throughput, also known as Ideal Speed (Actual Throughput / Ideal Speed). Sometimes operators want to run a line slower to reduce downtime or potential waste, but the reduction in downtime and waste by reducing speed doesn’t necessarily generate a higher Yield. But you won’t know that unless you start tracking Performance.
8. OEE (Overall Equipment Effectiveness)
OEE is a composite metric that combines Availability, Performance, and Yield to help evaluate how effectively a machine or specific equipment is operating relative to its capacity (Availability x Performance x Yield). Once you’re able to measure OEE, you’re able to look for areas of process improvement. For example, if you can reduce the time it takes to produce a product (increase Performance), OEE will increase because you’ll increase your output in the same period.
Increase Profitability
9. Total Manufacturing Cost per Unit
While it may seem intuitive that the top profitability KPI in operations would be Gross Profit or Net Profit Margin, manufacturers report that the Total Manufacturing Cost per Unit metric is more important for them to track. This makes sense because, if you want to increase your margin, you need to get a handle on the costs of manufacturing. Comparing the total of all controllable manufacturing costs for a production lot to the number of units produced in a production period will help a plant-floor operator know immediately the impact of wasted raw materials on the bottom line (Total Controllable Costs / Total Units). Are we operating cost-effectively or not?
10. Downtime
For every second your machine is down, profit is walking out the door. This is the mirror image of Availability (Time Not Running / Total Time). Simply reporting how much time is lost, though, is not sufficient. Feedback from operators at the time of the delay is key to capturing downtime reasons. You need to be able to identify the top reasons for downtime and top solutions used to address unplanned downtime to improve the process and consequently increase your profitability.
“Data is the Raw Material of Improvement”
One thing that should be obvious is that the only way you’ll be able to deliver these operational metrics is if you are already collecting the data. Bernie Smith couldn’t be more right when he wrote, “Process performance data is the raw material of improvement.”
In the world of manufacturing automation, plenty of vendors can help you collect data and implement real-time dashboards for the plant-floor and front-office. But there seems to be a lack of utilizing the volumes of historical data generated in conjunction with the real-time data, as well as a lack of being able to perform your own analysis of production over time. Implementing these KPI examples will not be possible without a strong data foundation.
We can deliver solutions that can provide both instant feedback as well as diagnostic, predictive, and ad-hoc analytics over time. We’d love to talk with you more about how we can help you get started.
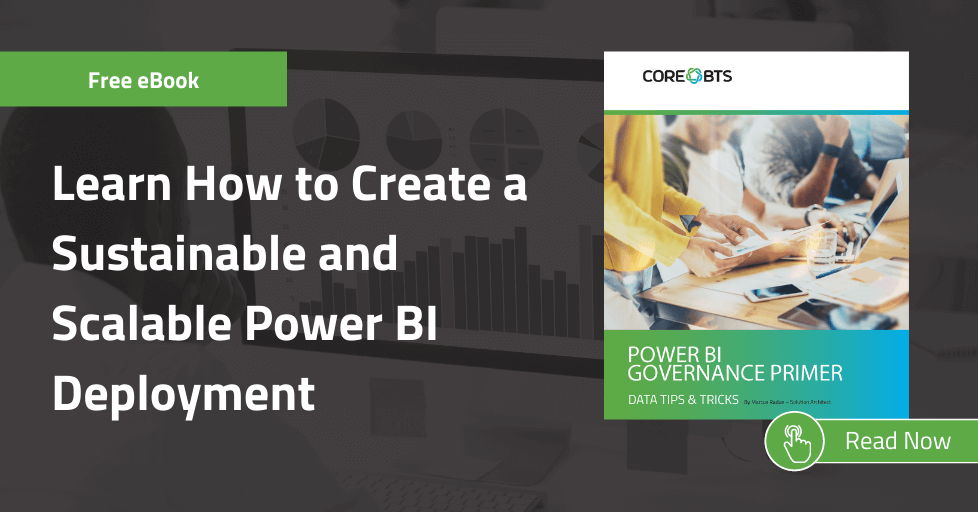