Industry 4.0 is transforming manufacturing practices and needs to be on the C-suite agenda. We unpack its advantages and how to get started with a tight IT budget and lean internal staff.
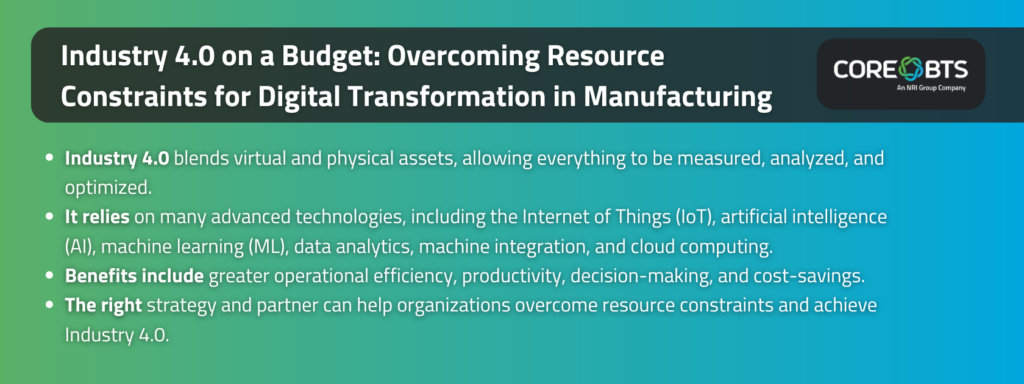
The much-heralded fourth industrial age, or Industry 4.0, is a reality, and it’s hard to overestimate its significance. The systems and technologies behind this revolution help manufacturers capture benefits across the entire value chain-reducing material loss, increasing production capacity, minimizing carbon footprints, enhancing employee satisfaction, and boosting service delivery lead times. These gains significantly improve competitive position.
However, embracing Industry 4.0 is not so easy-nearly 70% of transformation initiatives don’t progress past the pilot stage. So, it’s understandable why companies with limited internal teams, budgets, and infrastructure consider it out of their reach. Fortunately, there’s a solution. The right strategy and partner make it possible to overcome resource constraints and confidently navigate the merging of digital technologies into manufacturing and industrial processes.
Industry 4.0 Explained
Industry 4.0 is a shift from traditional manufacturing practices to smart factories. The idea is that enhanced digitization, automation, and connectivity improve processes across the entire value chain, leading to unprecedented agility, flexibility, productivity, and decision-making.
A differentiator of the fourth industrial revolution is blending virtual and physical assets, allowing everything to be measured, analyzed, and optimized. Many advanced technologies, including the Internet of Things (IoT), artificial intelligence (AI), machine learning (ML), data analytics, machine integration, and cloud computing, make this possible.
- IoT: Most physical assets in Industry 4.0-products, equipment, machinery, robots, devices-use RFID tags and sensors to provide real-time data about their location, performance, or condition and communicate with each other. This connectivity and mechanization lets companies track products and inventory, stay on top of consumer preferences, prevent equipment downtime, rapidly design and modify products, run smoother supply chains, and much more.
- AI, ML, and data analytics: AI and ML algorithms analyze raw data captured on the factory floor, across business units, and other sources, turning it into actionable insights to improve automation and decision-making. For example, analyses may predict the need for equipment servicing, allowing manufacturers to perform timely maintenance to boost efficiency and uptime. It may also highlight a change in customer preference, allowing manufacturers to build more personalized products.
- Cloud computing: Cloud technology allows the cyber-physical systems at the heart of Industry 4.0 to coordinate and communicate readily. At the same time, it facilitates more efficient storage, analysis, and processing of large data sets, improving flexibility and scalability.
- Digital twin: A digital twin is a virtual simulation of a real-world system, process, product, or machine based on data from IoT devices, sensors, and other objects connected to the internet. It allows manufacturers to understand, analyze, and optimize the maintenance and performance of industrial products and systems.
- Machine integration: Machine integration allows manufacturers to collect, process, and standardize data from equipment and connect it to shop floor systems, such as enterprise resource planning systems (ERPs)or manufacturing execution systems (MESs). This ensures that each system has the most effective data for automation and decision-making.
Why Manufacturers Must Move to Industry 4.0
A switch to Industry 4.0 is more than a technology upgrade. By eliminating silos and connecting operations and teams across the manufacturing landscape, businesses establish a more holistic and transparent way of doing business.
Operational efficiency is enhanced with better productivity, reduced downtime, and improved resource allocation. McKinsey estimates that digitally enabled factories improve labor productivity by up to 30% and reduce machine downtime by up to 50%. This efficiency extends to green initiatives where smart automation and data analytics help reduce waste, optimize energy use, and develop more sustainable products.
Industry 4.0 tools and technologies allow businesses to collect, analyze, and interpret large data sets, which means they can quickly gain actionable insights and make accurate and confident decisions.
Industry 4.0 strategies and tools give businesses the much-needed edge to thrive in today’s volatile and ultra-competitive landscape. Companies that fail to embrace it risk falling behind in market share, innovation, capabilities, and growth.
Industry 4.0 On a Budget
Making the leap to Industry 4.0 is a bold endeavor requiring heavy investment in smart technologies and technical expertise. Most companies with lean internal staff and tight IT budgets get discouraged and begin to think that perhaps Industry 4.0 isn’t for them. That’s a mistake, considering the possibilities Industry 4.0 unlocks. Overcoming the challenges of digital transformation usually means having the right strategy and working with the right partner.
Such was the case with Ernie Green (EG) Industries. Since 1981, this leading manufacturer has consistently delivered globally competitive critical components and extreme precision parts to companies in the automotive, industrial, consumer, and medical device markets. Their products range from transportation parts to high-precision components for robot-aided surgery systems, household durables, and more.
EG industries rapidly grew over the years. A side effect of this was data segregation across its manufacturing and administrative locations in the Dominican Republic and North America. Many of these locations also used outdated infrastructure despite a massive overhaul of aging equipment in 2010. Between these challenges and limited internal resources, EG Industries wasn’t confident they could achieve Industry 4.0-until they tapped Core BTS for help.
First, we executed Azure Accelerate (a cloud economics and assessment program) to identify where EG Industries was in its cloud migration journey. This helped us understand what it would take to achieve Industry 4.0 and charter an optimal path forward.
Next, we recommended that the client adopt Core BTS’s holistic “OneContract” model to maximize their Microsoft investment. This would ensure they receive the IT management, security, and advisory services needed for the migration.
Understanding the importance of stakeholder buy-in in digital transformations, CoreBTS helped craft a business justification for presentation to EG’s board. Upon approval, we followed up with a meticulous implementation that included cloud optimization, application modernization, and building EG’s Azure environment.
With Core BTS taking care of the technical details of Industry 4.0 migration, EG industries could focus on enhancing key competencies and maximizing new opportunities. The net result was a seamless transition that reduced costs and increased productivity for EG industries.
Navigate Industry 4.0 Migration With Core BTS
Core BTS is a full-service digital consultancy company that helps businesses reach defined outcomes using custom, integrated, cutting-edge solutions. No matter where you are in your Industry 4.0 transformation, we can meet you there and move forward together.
Read the full case study of how we helped EG Industries achieve Industry 4.0 with OneContract.
Share on